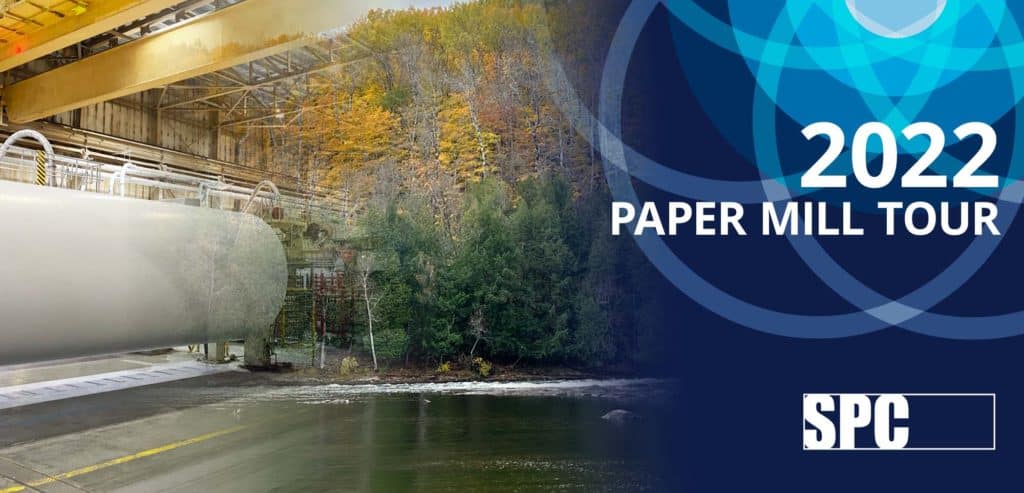
for the love of paper
Last month, SPC and a large group of clients hit the road to visit Billerud, Quinnesec Mill in Iron Mountain, Michigan. Client partners from coast-to-coast came to SPC to make the journey to Michigan’s U.P. The trip began at daybreak at the SPC headquarters in Niles, IL and by noon the group arrived, ready to learn, collaborate and bond over a common thread that ties them all together – paper!
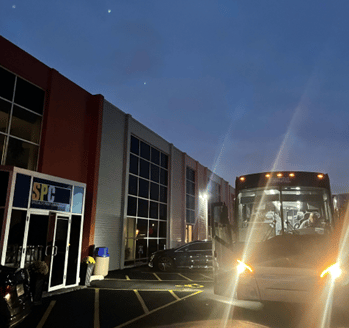
The Quinnesec Mill was the ideal location for the tour because of its scale, location in the Midwest, and the ability to see the entire paper-making process from pulp to paper. The mill is owned and operated by Billerud which has 10 production facilities the U.S. and Europe. Quinnesec, which began operations in 1985, encompasses 2,200 acres, and has one of the most advanced production environments in North America. A fully-integrated mill, producing its own woodchips, pulp, power source and, of course, all varieties of coated paper, was the main attraction.


The Right Wood Types Makes All the Difference
The Quinnesec Mill is known for producing some of the highest quality hi-maple hardwood kraft pulp in the world. Hardwood pulp is preferred for its tighter grain which allows for a more superb image quality during printing. The Quinnesec Mill produces lines like Influence®, Arbor Web®, Sterling Ultra®, Arbor Web Plus®, Sterling® Fragrance, Sterling Ultra C1S®, Anthem Plus®, and Blazer Digital®.

Equally as important as the quality of wood are the environmental assurances and guidelines followed at the mill. Paper mills require an abundance of two main ingredients: tree pulp and freshwater. Considering the importance of these natural resources, environmental advocacy is a top priority. Each day the mill uses 20 million gallons of water from the Menominee/Escanaba River, of which 19 million gallons are returned to the river after going through a rigorous water treatment process. This backwater actually exceeds both state and federal environmental standards. Air quality, water quality, and waste management/beneficial reuse are top priorities at Quinnesec.
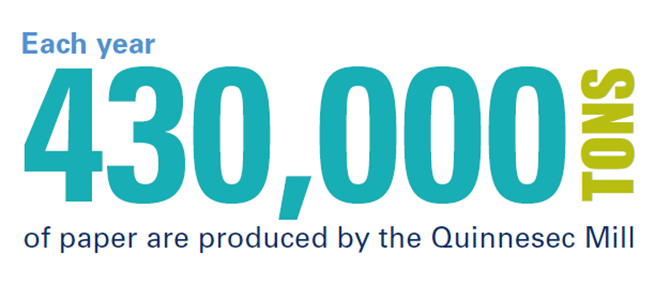
The Paper-Making Process at a Glance
Over the last few years, it has been difficult in obtaining paper due to supply chain shortages. Having the opportunity to see the process, from raw materials to the creation of the paper, is truly remarkable. At the Quinnesec Mill, they produce paper with a variety of finishes, from matte to gloss, all utilized in commercial printing applications. The process starts with the tree, hardwood tree species like maple, birch, and beech are most commonly used. 100% of the wood used at the mill is certified FSC®, PEFC®, and SFI®.
When the raw timber arrives at the mill, the first step is the debarking of the tree, meaning the timber elements are separated and the desired wood is broken up into small chips. The chips are processed in a digester that further breaks down the material into a pulp or paste that is then cleaned & bleached. When the pulp eventually arrives at the paper machine, the material is sprayed onto a forming section where the water is methodically extracted to form a continuous-length paper.
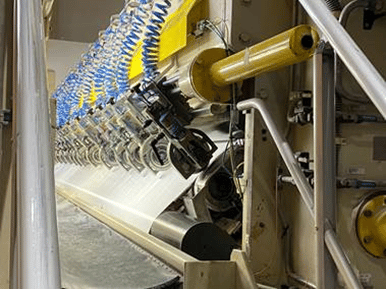
The paper then enters the drying phase where 35 dryer cylinders are used to evaporate the remaining water.
When the paper is nearly 100% dry, the sheet goes through the coaters. In this process, a uniform coating is applied to the sheet. The coating is like latex paint and is composed of clays, calcium carbonate, and titanium dioxide. Matte and soft gloss paper are also finished at this point. From here the paper is wound onto a spool after being cut to the proper width and diameter specified by the clients.
Innovation is Driving Efficiency and Sustainability
A huge technological advancement in the paper-making process is the use of smart systems in production. Smart systems have allowed operators to check pulp and paper conditions throughout the duration of the papermaking process. This creates more accurate and consistent results throughout production.
Big Data is being used to monitor market trends. This allows paper manufacturers to prepare for the needs of the market. By monitoring trends, paper producers can help with cost and time savings. Big Data is also used to track forest progress. When surveying land, surveyors can now monitor the lifespan of individual trees and determine exactly which trees are ready to harvest. This aids both the harvesting and replanting process.
“To see Billerud’s commitment to environmental sustainability was very inspiring and it helps support SPC’s commitments to our customers.”
Garry Nielsen, SPC

At the Quinnesec Mill, we witnessed and saw firsthand the craftsmanship, thoughtfulness, and stewardship of natural resources that left an indelible impression. There is a reverence and appreciation that we all share for paper. On our journey home allowed time for reflection, collaboration, and new friendships were formed over our common bond — paper.
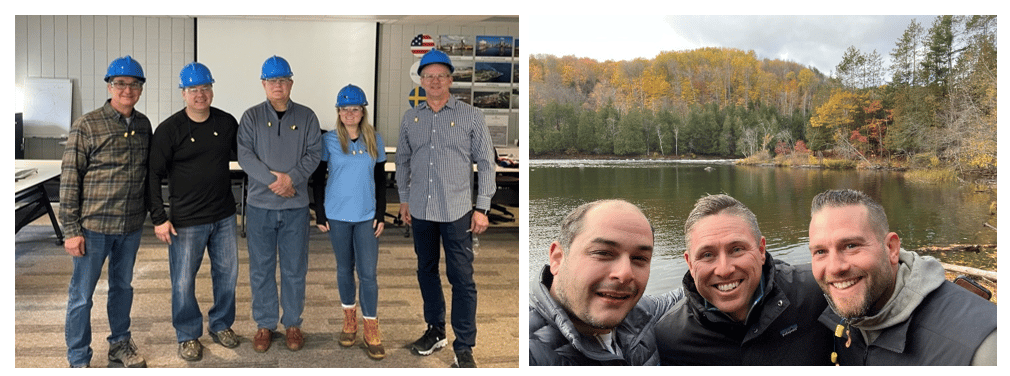