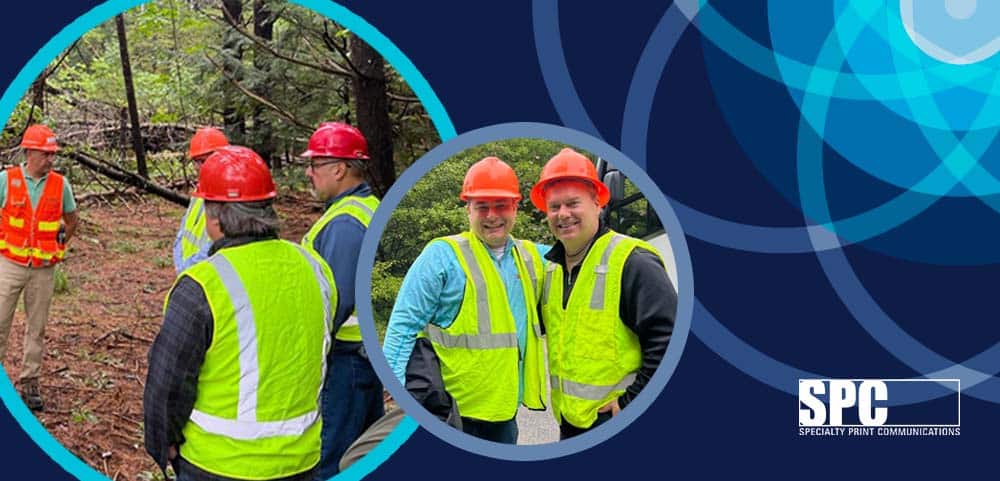
In mid-September, SPC and a large group of over 30 clients journeyed to the Sappi Somerset Mill in Skowhegan Maine, one of the largest paper mills in North America. The group was ready to learn, collaborate, and bond over a common thread that ties them all together – paper!
SPC clients got up close to see how various types of coated paper are created at a facility producing 970,000 tons of paper annually. Just as important, the group also got to witness all the efforts to make paper mills both economically and environmentally sustainable.
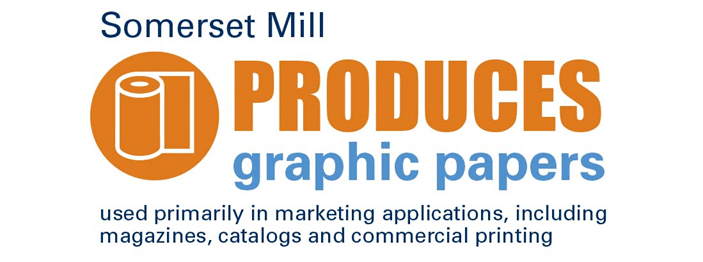
The Renewable Natural Source
Producing quality paper starts in the forest. Trees are carefully selected from nearby working forests and cut into 8-foot logs that are hauled to the mill. 75-80 trucks enter the facility each day carrying about 32 tons of harvested wood per truck. 100% of Sappi North America’s woodfiber inputs originate from controlled, noncontroversial sources selected within well-managed forests.
Sappi is certified under three different global certification systems: The Sustainable Forestry Initiative (SFI), the Programme for Endorsement of Forest Certification (PEFC), and the Forest Stewardship Council (FSC). These certifications provide mills with clear principles and standards to meet. Specific harvesting techniques are designed to minimize impacts on the forest such as supporting new tree growth through species diversity with canopy openings. These techniques allow the trees to constantly regenerate, ensuring forests remain healthy.
It is a common misconception that tree harvesting simply harms the environment. However, when looking from another angle, it’s clear the paper industry is committed to a net positive impact on the environment by implementing sustainable forestry practices that reduce greenhouse gas emissions and conserve and continually replace natural resources. The sustainable forest management standard ensures clean air and water and protects biodiversity.

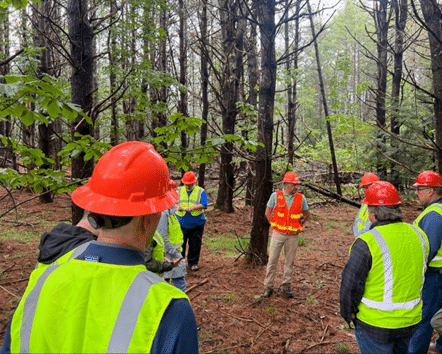
The Paper-Making Process at a Glance
Once trees are transported to the mill, the logs are efficiently debarked and chipped. A complex process using steam and heat continues to break down the wood fibers, eventually producing a big pulp soup. Separating the pulp that will be used to make paper, any remaining biomass is utilized to provide fuel and power for the mill.
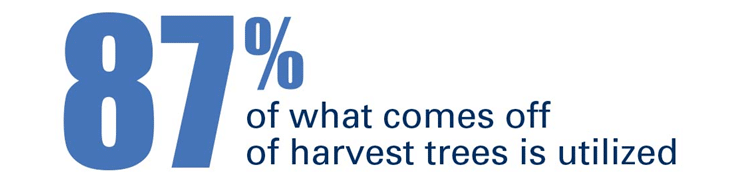
The pulp then heads to one of three enormous machine lines at Somerset. Spanning over two football fields in length, the paper machines work their magic by first extracting nearly all the water out of the “crude” paper product. Then the paper runs automatically through several stages such as bleaching, coating, and cutting into various sizes. It’s truly amazing to see the scale of these machines and the efficiency of the entire process.
An Amazing Experience
After the tour, the group was treated to the best that Maine has to offer. We visited the historic Portland Head Light in Cape Elizabeth to take in the iconic views of the coastline. The group also indulged in Maine’s most famous cuisine at a classic lobster boil.
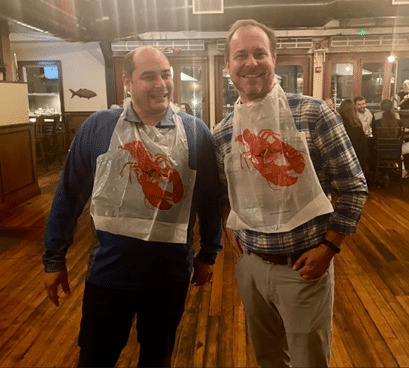

A primary takeaway from the Somerset Mill tour is the careful and committed stewardship of natural resources. It is important in our eyes to work with organizations that are leaders in shaping what responsible sustainability looks like in the paper industry.
SPC is grateful to have shared this opportunity with our clients. If you missed this experience, stay tuned for SPC’s next adventure!